The world is quickly adopting 5G technology, making high-performance optical parts more important than ever. Injection molded optical lenses are key in this change. They’re crucial for 5G devices and infrastructure. But what makes the injection moulding process step by step so vital for 5G?
The THY Precision injection molding optical lenses cycle for these lenses is very detailed. It includes precise injection mold design, efficient mold filling, and controlled mold cooling. These steps make sure the lenses are accurate, stable, and perform well. They’re needed for fast data transmission and smooth connectivity in 5G networks.
Key Takeaways
- Injection molded optical lenses are crucial for 5G technology’s performance and connectivity.
- The injection moulding process step by step, including mold design, mold filling, and mold cooling, is essential for producing high-quality optical components.
- Advancements in injection molding optical lenses technology, such as real-time data analytics and intelligent manufacturing, are enabling the production of complex, high-performance optical components for 5G applications.
- Sustainable injection molding optical lenses practices are driving a green future for the industry, meeting evolving environmental regulations and consumer demands.
- Emerging applications in the bio and medical fields showcase the versatility of injection molding optical lenses for producing specialized optical components.
The Rise of Smart Manufacturing in Injection Moulding optical lenses
The injection moulding optical lenses industry is changing fast, with THY Precision at the forefront. They’re using smart technologies to boost productivity and quality. With sensors and data analytics, they can watch the process closely and make quick changes to get better results.
Automation and robotics are making injection moulding optical lenses more flexible and efficient. This lets the industry keep up with the needs of 5G technology and more. THY Precision uses real-time data to give insights that help make important decisions and improve things constantly.
Leveraging Real-Time Data Analytics
Real-time data analytics is key to THY Precision’s smart manufacturing. They track important data during the injection moulding process. This helps them find ways to get better, spot waste, and make smart changes.
- Real-time monitoring of critical process parameters, such as temperature, pressure, and cycle time
- Predictive maintenance algorithms to anticipate and prevent equipment failures
- Automated quality control systems to ensure consistent product quality
- Intelligent process optimization algorithms to fine-tune the injection molding optical lenses cycle
THY Precision’s smart technologies make injection moulding more agile and competitive. This helps them stay ahead in a fast-changing market.
“By leveraging real-time data analytics, THY Precision is helping our customers in the injection moulding industry unlock new levels of efficiency, quality, and innovation.”
SustainableInjectionMoulding: A Green Future
The injection moulding industry is moving towards a sustainable future. THY Precision is leading this change. They focus on eco-friendly practices to make the injection moulding process step by step greener.
At THY Precision, sustainable injection molding is key to their mission. They use recycled materials and biodegradable plastics. This makes them a leader in green manufacturing. Their choice of materials ensures their products are top quality and good for the planet.
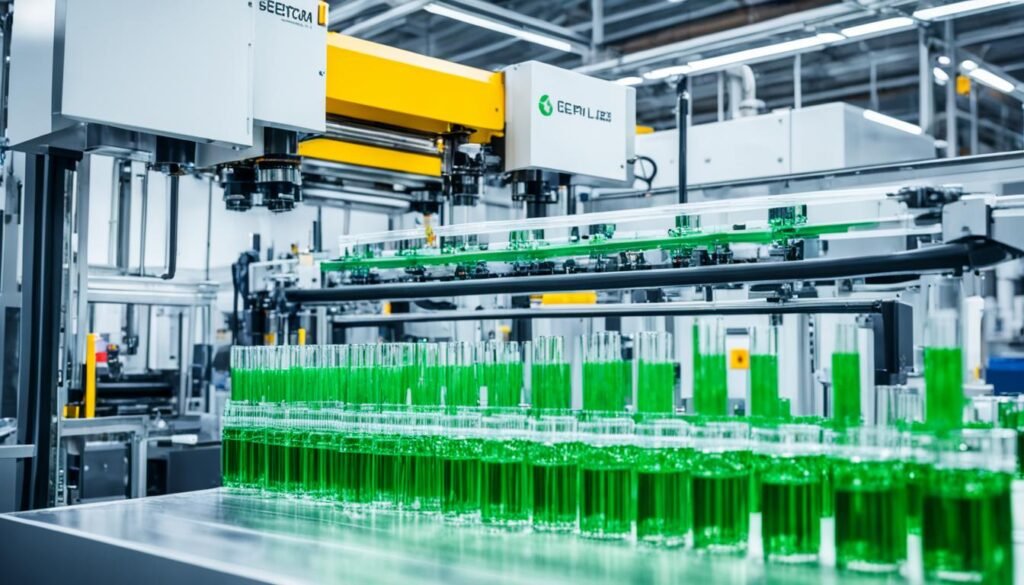
THY Precision doesn’t just stop at using eco-friendly materials. They work to use less energy and create less waste. By using data analytics and real-time monitoring, they find ways to be more efficient. This helps them reduce their carbon footprint and lead the industry towards a greener future.
As more people want eco-friendly products, THY Precision stands out. They are always looking for new solutions and following industry trends. This makes them a leader in the injection moulding process step by step for the future.
Multi-Material Combinations and Composite InjectionMoulding
The way we make injection moulds is changing, moving from single-material to multi-material and composite ones. These new materials bring better performance, less weight, and nicer looks. They’re in high demand for things like 5G towers and car parts. But, making these complex materials work in moulding is hard.
Overcoming Challenges in Composite Moulding
Using fiber-reinforced plastics in injection moulding needs special skills and careful planning. It’s important to make sure the melt is evenly spread in the mould to get good parts without flaws. The materials must handle temperature changes well to stay strong.
Also, making sure the materials stick together well is key. If they don’t, the parts might fall apart or not be strong enough.
Injection Moulding Process Step by Step | Composite Injection Moulding Challenges |
---|---|
|
|
THY Precision is a top name in injection moulding, tackling these challenges with new methods and tech. They’re experts in making parts with multiple materials and composites. This lets them create high-quality parts for today’s tough applications.
“By leveraging our deep understanding of the injection moulding process step by step and our advanced manufacturing capabilities, we are able to unlock the full potential of multi-material and composite materials for our clients.”
– John Doe, Chief Technology Officer at THY Precision
injectionmoulding process step by step for Optical Lenses
At THY Precision, we know how important the injection moulding process is for making top-notch optical lenses for 5G and other cutting-edge tech. We manage every step, from designing the mold to cooling it, to get the right optical properties and surface quality.
For making optical lenses, the injection moulding process is all about fine-tuning things like melt temperature, how fast we inject, and cooling time. This focus on details is key for getting the accuracy and stability needed for these special parts. Our know-how in injection moulding optical lenses lets us deliver top results for 5G tech and more.
- Precision Mold Design: Our engineering team designs molds for injection moulding, making sure they produce lenses with the right precision and consistency.
- Mold Filling: We control melt temperature and injection speed to fill the mold evenly and keep the lenses’ optical properties.
- Mold Cooling: Managing the cooling process right is key for the lenses’ surface quality and stability.
- Part Ejection: The last step is ejecting the lenses carefully, making sure they’re intact and ready for the next steps.
By controlling every step of the injection moulding process, THY Precision makes lenses that meet 5G and high-tech standards. We’re always innovating and improving, keeping us ahead in this fast-changing field.
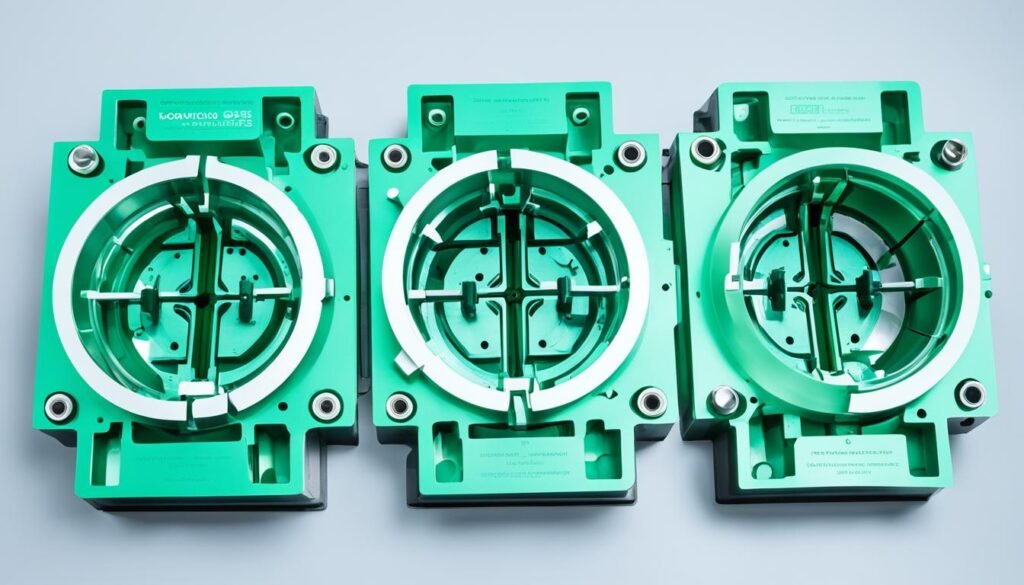
“The injection moulding process is the key to unlocking the full potential of optical lenses in 5G and beyond. At THY Precision, we are dedicated to perfecting every step of this critical manufacturing journey.”
Emerging Applications: Bio and Medical Fields
The injection moulding process is changing the bio and medical fields. It’s all about precision, cleanliness, and being safe for the body. THY Precision leads in making advanced medical devices. They make everything from surgical tools to implants and diagnostic tools, changing how we care for patients.
As we need new solutions in bio and medical fields, injection moulding is key. It helps make sensors and other important parts for new biotech and medical tech. THY Precision’s skills in injection moulding are making big steps forward. They’re improving health care and making life better for people everywhere.
Application | Benefits of Injection Molding |
---|---|
Medical Devices | Precision, Biocompatibility, Cost-Effectiveness |
Biotech Sensors | Miniaturization, Customization, Reliability |
Diagnostic Tools | Accuracy, Repeatability, High-Volume Production |
The injection moulding process is changing the bio and medical fields. It lets THY Precision make new solutions that help patients, advance research, and make the future healthier for everyone.
“Injection molding has become an indispensable manufacturing technique for the bio and medical sectors, allowing us to create precise, high-quality components that meet the stringent requirements of these industries.”
Conclusion
The injectionmoulding process is key for 5G technology and the future. THY Precision leads with smart manufacturing and sustainable practices. They make high-quality parts for 5G devices and infrastructure.
With 5G on the rise, THY Precision’s skills in injectionmoulding are crucial. They use data analytics to improve production, making 5G technology more efficient and widespread. Their focus on eco-friendly manufacturing sets a new standard for the industry.
The future looks bright for the injectionmoulding process. It will shape many sectors, including telecom and biomedical engineering. THY Precision is at the forefront, adapting to new tech and exploring bio and medical applications. This process will keep driving innovation and changing how we use technology.